Protection and prevention of accidents in the workplace.
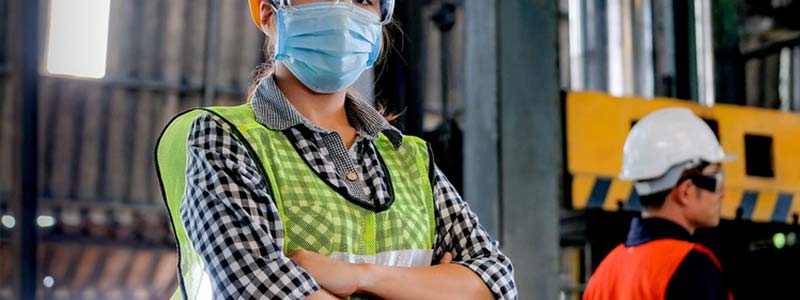
According to Law No. 3850/2010, businesses and organisations in private and public sector that employ even one employee are obliged by law to have a Safety Technician. The Safety Technician advises and suggests in writing in the Safety Technician’s book or orally to the employer and employees on matters relating to health, safety and the prevention of work accidents in the workplace.
More specific the Safety Technician:
- checks the safety of facilities and technical means before their operation.
- informs the supervisors of each department or the management of the company.
- inspects workplaces in terms of health and safety and reports to the employer or the manager of each department of the business.
- supervises the correct use of personal protective equipment.
- investigates the causes of work accidents and suggests appropriate measures to prevent accidents.
- Supervises how ready the personnel are to react in fire protection and alarm accidents.
The Safety Technician provides all the above when visiting the company according to the visit program submitted to the competent Labour Inspection.
The Occupational Risk Assessment Study is a main legislative obligation (L. 3850/2010, article 43) for all businesses in private or public sector, except for the country’s armed forces, regardless of the number of employees and their field of economic activity. It is the process of assessing the risks to the Health and Safety (OHS) of employees at work arising from the conditions when a source of risk occurs in the workplace and is one of the most basic tools for the best management of Occupational Safety and Health at work.
The Occupational Risk Assessment Study should generally contain the following points:
- Prompt diagnosis of occupational risks in the workplace and their prompt treatment, before they affect the operation of the company.
- Recognition of all burdensome work situations that make employees’ work tedious, unpleasant and inefficient.
- Prioritisation of professional risks (RISK ANALYSIS), as well as setting priorities to deal with them, according to national legislation, technological developments and company policy. In this way, unnecessary expenses are avoided.
- Harmonisation of the Occupational Risk Assessment with the requirements of the OHS Management System of the company, making it a ‘tool’ for taking measures in order to continuously improve Health and Safety in the working environment.
- Monitoring the implementation of the measures and revising them when necessary.
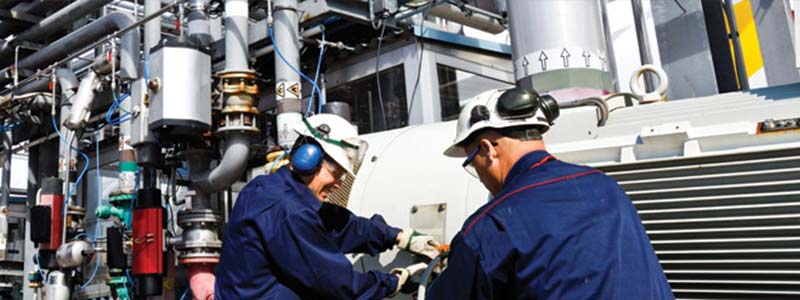
The «K&VGroup» company has developed a standard method for the preparation of the Occupational Risk Assessment Study, which is now a widely accepted methodology and meets the requirements of the European directives and Greek legislation. The method has been used successfully in hundreds of facilities of different sectors nationwide.
Our company consistently undertakes and runs responsibly all the required checks and informs employees and staff about the risks in the workplace in order to prevent accidents.
More specific, we undertake:
- Description of contents, equipment and building facilities
- Check for operating permits, fire protection certificate and equipment certifications, etc
- Ascertainment of the preparedness of the means of personal protection
- Risk assessment
- Moral hazard assessment
- PML and EML calculation
- Suggestions for risk improvement
The «K&VGroup» company has the ability to organise training days and seminars according to the needs and activity of a company, which fully cover the employer’s obligations (P.D. 17/96, No. 12), offering extra value to executives and employees.
The educational seminars are of an experiential nature. Through the interaction they offer the participant the necessary knowledge in Health and Safety as well as Industrial Safety. The goal is for your employee to be able to respond to the modern and demanding needs of your business.
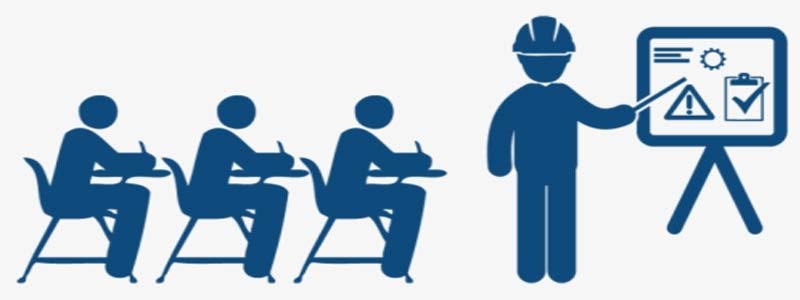
For every interested company we offer specialised seminars, which are presented on site or remotely in the following areas:
- Industrial safety
- First Aid
- Machine handling with safety
- Explosive environment –ATEX
- Transport of Dangerous Goods – ADR
- Fire protection – Fire safety
- Prevention of musculoskeletal diseases
- Ergonomics (offices)
- Safety in electrical installations
- Safe use of forklifts – pallet trucks
- Safe use of telescopic lifting mechanisms
- Safe use of cranes
In «K&VGroup» we believe that knowledge is ‘gold’ and should be imparted!
The «K&VGroup» company has the expertise to provide advice and options for every business need in terms of space signage. Workplace safety signage informs, alerts and finally prevents occupational risks to which staff are exposed. According to the P.D. 105/1995 the installation of a whole safety system is an employer’s obligation if the existing or potential risks cannot be avoided or reduced sufficiently with the technical means of collective protection or with measures, methods or work organisation procedures. Furthermore, safety signage is a high responsibility of each business towards the employees and visitors and contributes to creating the feeling of a well-organised and responsible business.
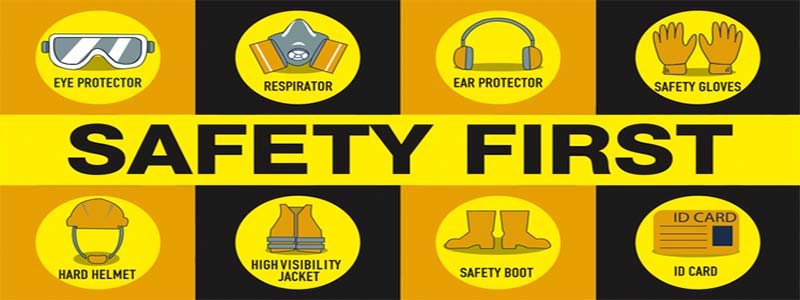
Our company, having knowledge and experience in the design and prevention of occupational risk, undertakes the study of the requirements of the workplace and the preparation of the Safety Signage Study of the premises. In this way, the requirements for means of signage are demonstrated and in accordance with ergonomic positioning principles, the final design is derived.
The types of signage are:
- Mandatory signage
- Informational signage
- Prohibition signage
- Safety signage